A un par de horas al oeste de Tokio en tren bala, en la ciudad de Mizunami, una escuela en desuso ofrece a las automotrices japonesas una educación muy peculiar. La empresa de ingeniería inversa Caresoft Global Technologies Inc. ha convertido el antiguo plantel en un laboratorio para el diseño de vehículos eléctricos. Allí desarma los automóviles para estudiar las innovaciones que contienen, elabora propuestas para ahorrar costos y las presenta a los fabricantes de coches. Algunos clientes que visitan el sitio estudian las piezas en salas que antes eran aulas; en un cubículo que antes almacenaba balones de voleibol, otros revisan datos obtenidos mediante rayos X de alta energía. Y en lo que solía ser el gimnasio, Toyota Motor Corp., el principal fabricante de automóviles del mundo, tiene buenas razones para estar preocupado.
Sobre el piso de duela descansan los restos de un Tesla Model Y, un BYD Seal y más de una docena de otros autos eléctricos. Al comparar sus partes, la métrica más importante es la reducción de peso. Para que el sector eléctrico siga creciendo, los vehículos necesitan competir mejor con los coches a gasolina en autonomía. Por lo tanto, casi todas las decisiones de diseño deben contribuir a que el auto sea más liviano. Como ejemplo básico, consideremos un componente: la pieza núm. 55330-42410 de Toyota, una barra de acero de 9 kilos conocida por los ingenieros como viga transversal del vehículo, cuya función es sostener el volante y el panel de instrumentos y proteger la cabina durante una colisión.
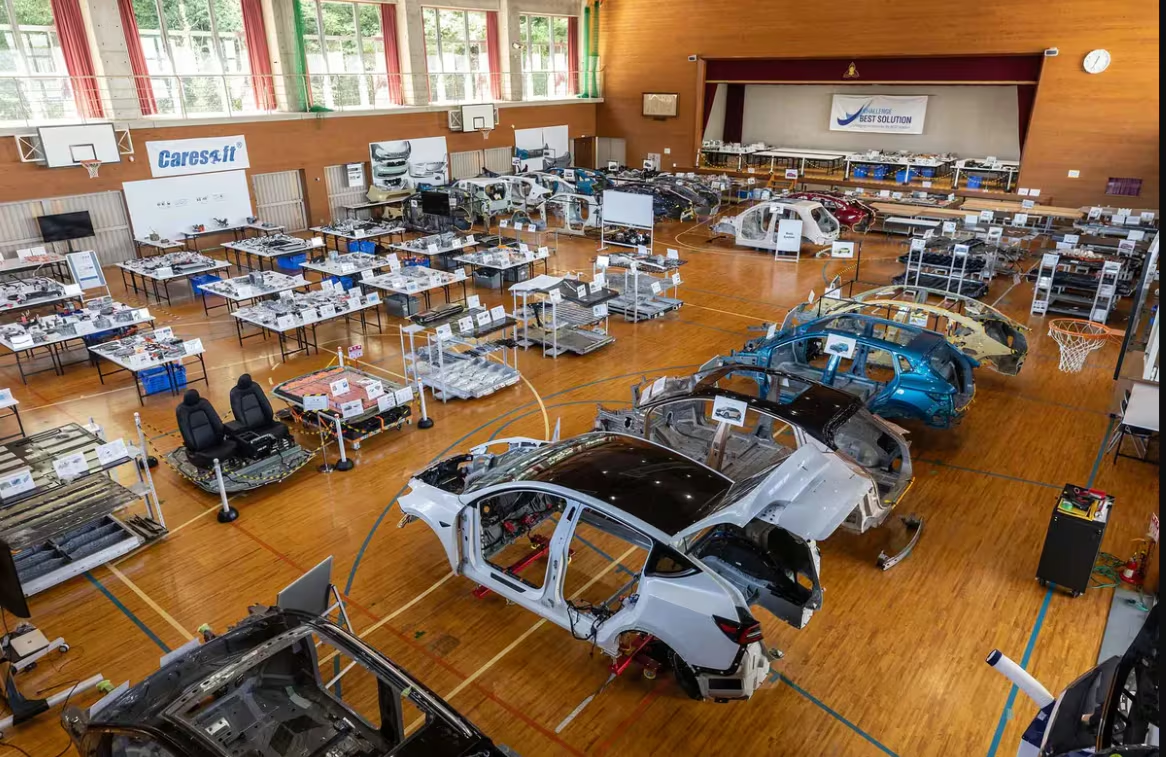
Esta pieza se encuentra dentro del bZ4X, el único automóvil totalmente eléctrico de la marca Toyota para el mercado masivo mundial, porque tiene un diseño probado que se usa en otros innumerables modelos. La viga transversal estándar de hoy es el resultado de mejoras incrementales realizadas a lo largo de décadas, y la mayoría de las versiones de dicha pieza han terminado bajo los capós de automóviles de combustión interna. La pieza es un testimonio del Sistema de Producción Toyota, que continuamente perfecciona hasta los detalles más mínimos de las piezas individuales del automóvil. A lo largo de incontables iteraciones, la viga ha sido diseñada para evitar que los pasajeros sientan las vibraciones de un motor de combustión interna.
La clave para los eléctricos
Pero los motores eléctricos no vibran y además el acero es pesado. Por esta razón Tesla y BYD, los principales fabricantes de vehículos eléctricos a batería, producen vigas similares pero de plástico. Las suyas pesan unas 6 kilos, según Caresoft, y también son más baratas y fáciles de instalar.
Es un cambio que suena muy simple una vez que lo escuchas, y hasta intuitivo si nunca has lidiado con un motor de gasolina. Pero si has pasado toda tu vida pensando en términos de micromejoras (el método kaizen, la filosofía que sustenta el Sistema de Producción Toyota o TPS), es una idea que bien podría resultar esquiva. “El kaizen no te llevará de un vehículo con motor de combustión interna a un vehículo eléctrico de batería, ese es el dilema de Toyota”, advierte el presidente de Caresoft Terry Woychowski, exejecutivo de General Motors Co.
El éxito de Toyota
Fuera del segmento de los vehículos eléctricos, Toyota no solo va bien, va estupendamente bien. Aunque va a la zaga (incluso de competidores de la vieja escuela) en la transición de sus líneas de producción a modelos totalmente eléctricos, el año pasado esa situación le favoreció. Si bien la demanda de autos eléctricos siguió creciendo, no lo hizo tan rápido como la industria automotriz de 3 billones de dólares había esperado mientras invertía miles de millones de dólares en su desarrollo. Entre tanto, los productos de Toyota estaban constituidos por dos tercios de automotores de combustión interna, un tercio híbridos y 0.1 por ciento eléctricos, y la compañía reportó ganancias récord. Se distanció aún más de sus eternos rivales (Volkswagen, Hyundai, GM) y se estima que en 2024 vendió más de 11 millones de vehículos, frente a los 4.3 millones de BYD (1.8 millones de ellos eléctricos) y 1.8 millones de unidades de Tesla. El presidente Akio Toyoda ha insistido en una “estrategia de múltiples vías”, que en la práctica ha significado vehículos híbridos, a gasolina e incluso autos propulsados por hidrógeno. Aunque Toyoda, que tiene 68 años, cedió en 2023 el papel de director ejecutivo al exjefe de Lexus, Koji Sato, la palabra del presidente sigue siendo la que importa.
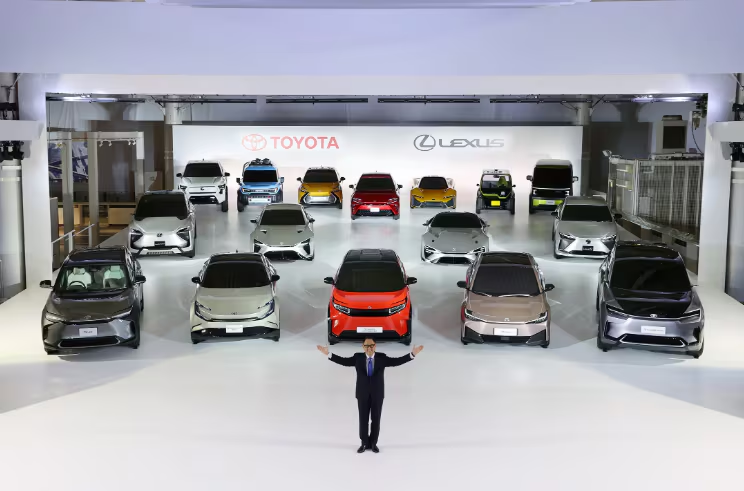
“Los 11 millones de unidades de Toyota son la suma total de tener clientes en varios países y muchos modelos”, comenta Tatsuo Yoshida, analista de Bloomberg Intelligence. “Mantener ese nivel de producción no es nada fácil. A muchas otras automotrices les resulta difícil superar los 6 millones”. La compañía no ha registrado pérdidas desde 2009 (justo antes de que Toyoda asumiera la presidencia) y ha superado una serie de contratiempos desde entonces.
Sin embargo, a largo plazo, la aversión de Toyoda a un replanteamiento fundamental del negocio puede limitar la capacidad de la compañía para imaginar los autos del futuro. El TPS o Sistema de Producción Toyota ha influido para que la armadora (y sus imitadores en todo el mundo) aísle a sus ingenieros especializados, se concentre en optimizar los procesos de montaje y externalice la mayor cantidad posible de componentes a proveedores externos. Estas medidas la han ayudado a maximizar las eficiencias de un mercado de hardware maduro y homogeneizado. Empero, para un hardware que apenas está en sus comienzos, a menudo son un lastre.
Tesla y BYD han logrado que sus plantas productivas sean más económicas y modulares, al tiempo que se afanan en producir más piezas internamente. Esto se debe en parte a que están diseñando nuevos componentes o combinaciones que no existen en el inventario de los proveedores (un coche eléctrico típico tiene unas 11 mil piezas, según ha estimado Goldman Sachs Group Inc., alrededor de dos tercios menos que su equivalente de gasolina). También lo hacen para conservar más de su tecnología patentada, un tema que apenas ha preocupado a los ejecutivos de la industria automotriz tradicional. Esa tendencia hacia las autopartes propias significa que quienes las adoptan más tarde, incluso si tienen mucho dinero, encuentran más difícil simplemente copiar y mejorar las cosas que los pioneros concibieron. “A menos que adoptemos una nueva forma de pensar, nunca podremos ponernos al día”, afirma Shinichi Sasaki, ex vicepresidente ejecutivo de Toyota que ahora dirige la Unión de Científicos e Ingenieros Japoneses.
En respuesta a las preguntas para este artículo, Toyota dijo que su filosofía de producción va más allá del diseño de piezas y los procesos de fabricación y que encarna una voluntad de aprender de los errores y de cualquier fracaso. “Vemos las mejoras como oportunidades de evolución”, dijo en un comunicado Aki Irie, director general de asuntos públicos de la empresa. “El TPS es una forma de pensar, no solo un método para mejorar la eficiencia”.
Retos a superar con los eléctricos
A principios de enero, en el marco de la feria tecnológica anual CES en Las Vegas, el director de tecnología de Toyota, Hiroki Nakajima, dijo a Bloomberg Businessweek que su empresa estaba bajo presión, pero estaba decidida a superarla. “Una gran amenaza en este momento son nuestros competidores chinos, pero nos gustaría mejorar nuestra tecnología para superarlos”, apuntó antes de añadir: “el ochenta por ciento de la tecnología es fácil de reemplazar, pero el 20 por ciento restante es el más importante”.
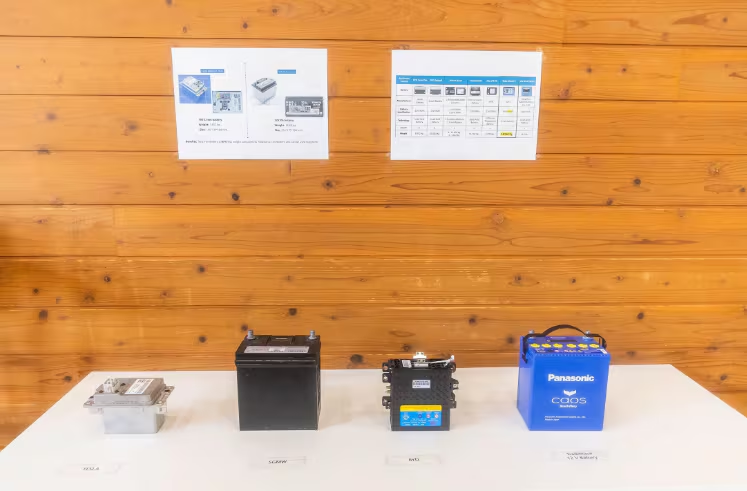
En el antiguo gimnasio escolar en Mizunami, parece claro que el futuro eléctrico requerirá algunos cambios que son impensables bajo el estricto paradigma del kaizen y el TPS. Tesla, por ejemplo, ha atornillado sus asientos directamente al paquete de baterías, que cumple una doble función como componente estructural. Mientras otras armadoras acoplan la batería al puerto de carga con un grueso cable de cobre y remaches, Tesla ha reducido el tiempo de instalación utilizando un cable de aluminio rígido. A su vez, la pieza #KTZ55X55S-A de BYD, de fabricación propia, combina en un solo módulo lo que solían ser ocho componentes del tren motriz eléctrico. Eso incluye hardware y software integrados para funciones como la gestión de la batería y la inversión de corriente (para transformar la corriente continua en alterna).
Ese sistema combinado pesa y cuesta aproximadamente un 20 por ciento menos que los componentes separados, de acuerdo con la firma de análisis Yole Group, que señala que BYD fabrica el 40 por ciento de sus piezas. “¡Madre mía!, ellos hacen todo: fabrican sus propias baterías, fabrican sus motores, su propia carrocería, fabrican sus fascias delanteras y traseras, sus faros, los paneles de las puertas, sus consolas. Es un salto cuántico. Eso no se consigue con kaizen”, dice Woychowski, el presidente de Caresoft.
La evolución de Toyota
Toyota nació de un salto manufacturero diferente. Hace un siglo, Sakichi Toyoda, el bisabuelo de Akio, inventó un telar mecánico que podía intercambiar por sí solo los carretes de hilo y también detectar si el hilo se rompía, deteniéndose automáticamente hasta que un trabajador corrigiera el problema. Cuando Sakichi fundó su empresa, su fábrica de tejidos, en el centro de Nagoya, funcionaba con carbón. A finales de la década de 1930, todos los telares funcionaban con motores eléctricos (lo que los hacía más eficientes y fáciles de reparar), y el hijo de Sakichi, Kiichiro, había utilizado su experiencia con las cadenas de montaje para fundar una empresa automovilística. A finales de los años cincuenta, el suburbio de Nagoya donde Toyota tenía su sede había sido rebautizado como ciudad Toyota, y luego vino el dominio del mercado global.
Por décadas, la industria se reconfiguró siguiendo las pautas trazadas por la familia Toyoda, haciendo que las líneas de producción fueran lo más eficientes posible y concentrándose obsesivamente en reducir los costos. Hubo un tiempo, por ejemplo, en que las automotrices empleaban legiones de trabajadores para reparar los defectos de los automóviles después de que salían de la línea de montaje. Eso por lo general ya no sucede. De sus telares, Toyota exportó la idea de solucionar los problemas tan pronto como los trabajadores los detectaran, en lugar de esperar hasta que los automóviles estuvieran completamente construidos.
Hoy, muchos de los estándares de Toyota siguen siendo estándares de la industria. Durante una reciente visita a la fábrica de camionetas F-150 de Ford Motor Co. en Dearborn, Michigan, la línea de montaje estaba llena con las pioneras pantallas de monitoreo de Toyota, y un tablero de resolución de problemas etiquetado como “Kaizen” se encontraba justo al lado de la planta. Cuando se trata de producción en masa de alta calidad, “el objetivo es avanzar muy rápidamente para alcanzar a Toyota”, indica el director de operaciones de Ford, Kumar Galhotra. En Japón, Toyota es la compañía más valiosa en la Bolsa de Valores de Tokio.
En 2010, un año después de que Akio asumiera el timón, Toyota compró una participación del 3 por ciento en Tesla por 50 millones de dólares. En 2016 se deshizo de lo que conservaba de dicha participación, argumentando que quería centrarse en la construcción de sus propios vehículos eléctricos. Sin embargo, casi una década después, Tesla es mucho más valiosa (con una capitalización de mercado que ronda los 1.3 billones de dólares) y la presencia de vehículos eléctricos de Toyota asciende a solo tres fábricas que todavía fabrican mayoritariamente otros tipos de automóviles.
Esto ha obligado a los ingenieros de Toyota a utilizar algunas soluciones alternativas muy poco kaizen para las numerosas cosas que son fundamentalmente diferentes en la producción de vehículos eléctricos y que deberían requerir mucho menos espacio y menos personas. En determinado momento, la carrocería del bZ4X se desvía de la línea de ensamblaje principal para instalarle sus paquetes de baterías antes de volver a incorporarse a la línea principal, lo que ocupa espacio y tiempo adicionales. “¿Es la línea más eficiente? Probablemente no”, admite Susan Elkington, la principal ejecutiva de fabricación de vehículos eléctricos de Toyota en Estados Unidos. “Pero no puedes simplemente desmontar un sistema transportador y moverlo de un día para otro. Esa flexibilidad es muy importante a medida que hacemos esa transición y a medida que la tecnología cambia”.
En el desarrollo de procesos para fabricar vehículos eléctricos, los especialistas en automatización de Toyota están atados de manos hasta que la empresa se comprometa a construir fábricas exclusivas para los nuevos diseños. Mike Cicco, jefe de operaciones en Estados Unidos de Fanuc Corp., el rey de la robótica industrial, señala que las plantas más antiguas son menos aptas para incorporar nuevos procesos de fabricación, lo que deja a las empresas “un poco limitadas” a la hora de ajustar sus líneas de montaje. Toyota también ha tenido problemas en los departamentos de diseño e ingeniería. En 2022, un año después de introducir al mercado su bZ4X eléctrico, tuvo que llamar a revisión a miles de unidades porque las ruedas se aflojaban constantemente; sus desarrolladores no habían entendido del todo cuánto torque generarían los motores eléctricos y utilizaron pernos que no soportaban la tensión.
Fue un recordatorio incómodo de que la filosofía perfeccionista de Toyota no siempre se ha trasladado a sus coches. Los primeros años de Akio Toyoda en el cargo se caracterizaron por retiradas masivas de vehículos por motivos de seguridad, y en 2010 el gobierno estadounidense alegó que los Toyota defectuosos podrían haber contribuido a la muerte de casi cien personas. Años después, la empresa admitió haber mentido a clientes y reguladores y aceptó pagar una cifra récord de mil 200 millones de dólares como parte de un acuerdo en tribunales.
En junio de 2024, el Ministerio de Transporte de Japón amonestó a Toyota, junto con Honda y Mazda, por falsificar y manipular los datos de seguridad de sus vehículos al solicitar la certificación gubernamental. Para empeorar las cosas, una serie de filiales y subsidiarias de Toyota también admitieron haberlo hecho, lo que provocó suspensiones en la producción mientras los ingenieros implementaban las pruebas de certificación obligatorias. En una conferencia de prensa con motivo de la irregularidad, el presidente Toyoda hizo una reverencia en señal de disculpa, el primer imperativo de todo ejecutivo japonés de una empresa atrapada en un escándalo. Pero las disculpas terminaron tan pronto como comenzaron las preguntas de los reporteros.
Cuando un periodista le preguntó si la debacle significaba que la filosofía de producción de Toyota estaba llegando a sus límites, Toyoda lo miró con frialdad y respondió: “Eso es completamente erróneo”. Su equipo estaba trabajando duro, dijo, utilizando los principios kaizen para resolver cualquier problema que pudiera surgir, como siempre lo había hecho.
Toyoda ha defendido ferozmente su estrategia de múltiples vías como una respuesta que se ajusta a lo que demanda el consumidor, pero también hay algo personal en ella. Aparte de su legado familiar, es un fanático de los autos de carrera y, como dijo en el Salón del Automóvil de Tokio hace algunos años, ama “el olor a gasolina y el ruido”. Su empeño por seguir fabricando automóviles tradicionales deja a Koji Sato, el nuevo CEO, con la complicada encomienda de asegurar el futuro de la compañía sin cambiar a fondo su presente.
El nombramiento de Sato fue inteligente y “reconoció la necesidad de dar paso a la próxima generación”, opina Jeffrey Liker, profesor de ingeniería industrial en la Universidad de Michigan y autor del libro The Toyota Way. Sato es “una persona más joven y un ingeniero muy competente, con un historial de lograr desafíos que parecen imposibles”. Liker subraya la participación de Sato en el desarrollo de los primeros híbridos de Toyota y, más recientemente, el cupé deportivo LC de Lexus.
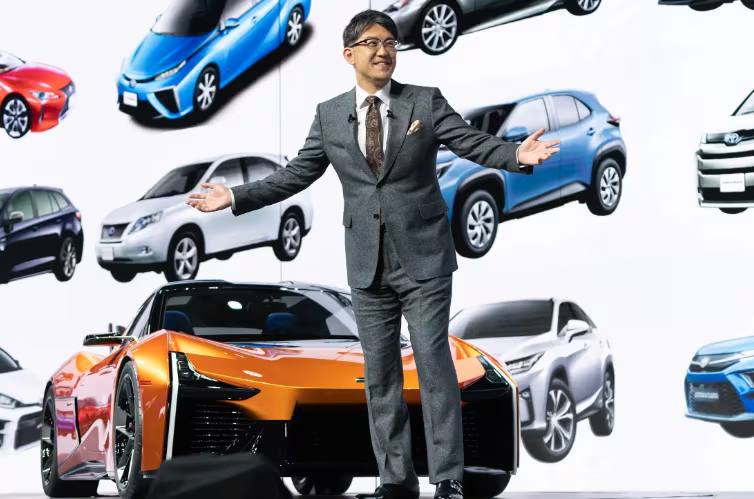
Cuando asumió el puesto de CEO en 2023, Sato prometió que Toyota vendería 1.5 millones de automóviles eléctricos a batería en 2026. A estas alturas, eso parece más una fantasía. Sin embargo, los vistazos ocasionales al interior de las instalaciones de Toyota sugieren que la compañía sí tiene algo parecido a un plan de acción. Durante una visita de prensa en 2023 al centro de investigación de la compañía cerca del monte Fuji, los ingenieros mostraron baterías de estado sólido de mayor autonomía, prototipos de sistemas de conducción autónoma y un automóvil eléctrico experimental diseñado para lucir y sonar como un auto deportivo a pesar de tener cuerpo de sedán. Junto al embrague, el pedal de acelerador estaba conectado a una bocina que reproducía sonidos de vroom-vroom al cambiar de marcha, imitando vagamente a un coche de carreras. Sato también ha autorizado gastos de miles de millones de dólares destinados a la producción de baterías y la modernización de las tres plantas donde Toyota fabrica vehículos eléctricos, una en Japón y dos en Estados Unidos (además, está en conversaciones para construir una nueva planta en China para fabricar modelos eléctricos de la marca Lexus, según ha informado Bloomberg News).
La planta japonesa que fabrica vehículos eléctricos, Motomachi, está a unos 10 minutos en coche de las oficinas de Toyota. Durante una visita de Businessweek este verano, vimos un bZ4X gris que avanzaba por una línea de montaje mientras los empleados instalaban asientos, cableado y componentes de la transmisión. Dos trabajadores colocaron la batería de casi 500 kilos en una coreografía fluida que duró poco más de 90 segundos. Las piezas venían en contenedores que salían de áreas de montaje paralelas, y había pantallas digitales en lo alto mostrando el estado de cada paso del proceso de armado. Sin embargo, cuando el bZ4X estuvo listo para pasar a la siguiente fase, la línea volvió a funcionar como de costumbre, ensamblando un sedán híbrido Crown y luego una minivan Noah a gasolina.
Si hablas con cualquier persona de Toyota te dirá que construir múltiples vehículos en la misma línea de ensamblaje ejemplifica el TPS, dándole a la empresa la flexibilidad de construir diferentes modelos en respuesta a las cambiantes demandas del mercado. “Al mezclar diferentes tipos de vehículos sin mantener inventario, la carga de trabajo para los proveedores también se equilibra y nivela”, explicó Irie en el mencionado comunicado.
Toyota no es la única que está teniendo problemas en prepararse para el futuro. GM, el líder entre los tres grandes fabricantes de Detroit, ha dado marcha atrás a su promesa de vender solo eléctricos para 2035. Ford, que ha creado una división eléctrica separada, ha puesto en pausa parte de su estrategia de vehículos eléctricos. Y Volkswagen AG está invirtiendo 5 mil millones de dólares en la startup eléctrica Rivian Automotive Inc., pero los resultados no llegarán pronto. Rivian ha estado perdiendo un promedio de 39 mil dólares por cada vehículo que vende.
Existe, por supuesto, un precedente del liderazgo de Toyota en este ámbito: el Prius. Quienes crecieron con un Prius difícilmente pueden imaginar lo revolucionario que fue a finales de los años noventa combinar un motor de gasolina con un motor eléctrico para obtener casi 50 millas por galón en un automóvil para las masas. Las complicaciones añadidas duplicaron el costo del sistema de propulsión en comparación con los modelos convencionales y garantizaron que, durante años, Toyota perdiera dinero con cada híbrido vendido. Esta decisión fue, en muchos sentidos, aparentemente contraria al TPS. Pero Hiroshi Okuda, el reformador que fue presidente y luego titular del consejo directivo de Toyota durante aproximadamente una década (de 1995 a 2006), presionó para invertir dinero en diversificar la tecnología y la presencia de la empresa.
Okuda ha desaparecido en gran medida de las historias oficiales de la compañía. Dimitió al oponerse a que la familia Toyoda volviera a tomar el control. “La industria automotriz japonesa ha podido convertirse en líder global, pero ahora está a la defensiva”, dice el ex director ejecutivo de Nissan Hiroto Saikawa. “No se le da bien replantearse las cosas de manera fundamental y aprender de eso. Pero ningún otro país tiene un conjunto tan amplio de ingenieros de tal calidad. Con una mente abierta al aprendizaje, aún podrán hacerlo muy bien”.
Hoy hay un Toyoda al que se le ha encomendado pensar con audacia. Daisuke, el hijo de Akio, es vicepresidente sénior de una subsidiaria que trabaja en tecnología de conducción autónoma y otros proyectos a largo plazo. Pero ahora mismo esa no es la ruta de Toyota. Al contrario, a principios de este año la compañía anunció que está desarrollando una clase completamente nueva de motores de combustión interna que algún día podrán funcionar con diferentes tipos de combustible líquido, incluidos los más limpios como el hidrógeno. Toyota dice que el menor tamaño y la mayor potencia de dichos motores los harán ideales para los híbridos de próxima generación.
“Sabemos que habrá críticos que pregunten ‘¿Por qué ahora?’”, dijo en primavera Hiroki Nakajima, el director de tecnología. “Sabemos que los vehículos eléctricos son el futuro. Pero hasta que lleguemos allí, seguiremos intentando mejorar en lo que mejor sabemos hacer”.
—Con la colaboración de Tsuyoshi Inajima y Nicholas Takahashi
Lee aquí la versión más reciente de Bloomberg Businessweek México: